Log in
Search
Latest topics
» Fox .35 Modifications by aspeed Today at 8:06 pm
» Happy Anzac Day!
by 706jim Today at 6:44 pm
» Project Cox .049 r/c & Citabrian Champion
by MauricioB Today at 4:08 pm
» Jim Walkers FireBee - This is going to be fun
by rsv1cox Today at 3:56 pm
» Revivng Some Childhood Classics
by rsv1cox Today at 7:17 am
» Introducing our Cox .049 TD Engines
by getback Today at 6:20 am
» Roddie's flat-bottomed boat..
by Levent Suberk Today at 12:23 am
» Cox powered jet-pump for model Sprint Boat
by roddie Yesterday at 10:25 pm
» Micro Draco Gets to Fly on a Beautiful Morning.
by rdw777 Yesterday at 8:15 pm
» Jim Walker Firebaby
by rdw777 Yesterday at 8:06 pm
» Hydro-bat by Vic Smeed: engine probs
by GallopingGhostler Yesterday at 5:12 pm
» Roddie-Rigger.. a 2005 original design
by roddie Yesterday at 3:39 pm
Cox Engine of The Month
Micro 12VDC Generator with a Cox .049 Sure Start Diesel Engine
Page 7 of 31
Page 7 of 31 • 1 ... 6, 7, 8 ... 19 ... 31
Re: Micro 12VDC Generator with a Cox .049 Sure Start Diesel Engine
Or a gear on the output shaft that turns another gear which has a pulley bolted to its face.StevenStanleyBayes wrote: Finding elastic tape and trying to run the alternator without too much of a force by the belt because the more the belt pull the higher the wear on the crankcase axel housing
I have an idea of how to decrease the wear of the crankcase axel housing : I do not know whether I can do but a company can easily manufacture a wheel with a rubber tire. The " tire " goes inside the pulley canal ( just like the belt ) where there is no belt. This wheel is " empty " and does not rotate anything. The only thing this wheel does is counters the pull of the belt which pulls the spinning crankshaft axel in the direction towards the dynamo. The empty wheel position and counter tension can be made adjustable by moving the wheel towards the engine pulley or away before securing the wheel with a screw or nut, just like a car alternator. Also, the wheel tension can be defined by a spring which moves the wheel towards the engine pulley. The strength of the string can be selected. The wheel can be mount on a movable arm, controlled by the spring.
Rusty
_________________
Don't Panic!
...and never Ever think about how good you are at something...
while you're doing it!
My Hot Rock & Blues Playlist
...and never Ever think about how good you are at something...
while you're doing it!
My Hot Rock & Blues Playlist
RknRusty- Rest In Peace
- Posts : 10869
Join date : 2011-08-10
Age : 68
Location : South Carolina, USA
Re: Micro 12VDC Generator with a Cox .049 Sure Start Diesel Engine
RknRusty wrote:Hey Steve, it sure is good to see it running. Rod's funny too isn't he Lol.
Okay, got grits on the burner so I could only watch up to 11:48. I'd like to make some suggestions.
First, it may not be a problem, but shorten your fuel line as much as possible without kinking it. Especially the big bottom loop so it's not fighting gravity.
Next is from start to stop I see you being too aggressive with the machine. Starting with the windup, it looked like you were wrapping it 1-1/2 or 2 turns. You may find better results with one turn. On some glow engines that are being especially contrary, I have found many times that 1/2 turn gets results when more won't do anything to ignite a charge.
The next thing I saw is your adjustments are very rapid. "Tweaking" means really considered and methodical. Once you get it running, make small adjustments and wait for it to adapt to your change in mixture, air, or compression. Temperature changes slowly compared to your twisting on the F/A mix, and it's just as much of a component as fuel, compression, and air. So you have to wait for it all to catch up.
I'm guessing that's the air valve to the intake on the long snorkel I see coming out of the top? Everyone has to learn these things when first getting the hang of it, and no two engines will act the same, so it's hard, but breath deep, make calm moves and you and it become a team. And get a box of Snoopy bandaids like I have near my table all the time.
Rusty
EDIT: I'be been writing this for an hour while I cook supper, and I see other replies. If I'm contradictory or redundant anywhere, I'll get back to it later.
Time for chow!
Rusty
Double Edit: Nevermind, those were all your own replies.
As usually, you are 100% right and everything you say is extremely useful! Thanks a lot for your replies and help.
I am sorry you are into Nitro and not diesel. I was to get much more help although others had helped a lot too. However, although diesel is more powerful, Nitro is the correct fuel for this project. This is because a rechargeable battery with the necessary circuit ( usually sold as a ready to use IC ) can do the job of starting up and be used longer. The most important feature of Nitro is customer friendliness. I saw videos on YouTube where people put the engine next to compression and then, with the battery on, just turn the " knob " on the propeller just slightly, say one eighth turn, and the engine start. Much easier than turning the key of a key start car ( I am not sure whether these are still manufactured as everything is with a button now ). And the engine is on, up and running. This is what customers want. However, I have already started with diesel and I will continue and, then, everyone can realise what the project would be with a Nitro engine. Besides, Nitro fuel is sold readily available in almost any country in the world whereas Davis Diesel is sold only in some countries and The UK is the only country in the world I have heard of where they sell all of the ingredients of a diesel fuel and very inexpensively.
I am happy to hear you suggest only one spring turn. Cox does too. I have never tried 1 turn but I must. The reason is I cannot even think of a possibility to start with 1 turn but I must as everyone says this is easier to start. I promise I would try as long as I do not forget.
You are 100% right on the length of the fuel line : must be as short as possible and, I think, shortening will definitely help. The reason to be so long is because I used the maximum allowed ( 10cm ) before I positioned the tank and I did not know where and how exactly to position the tank then, so I got 10cm fuel line with the idea to cut after and I did not. I must, though.
You are right with the rapid tweaking too. Must not be done and does not show anything because the engine must be able to reliably work with a given settings over a long period as the engine may perfectly OK work with some settings for a few seconds and then stop. I mixed only 10mL of fuel and wanted to run many scenarios to achieve low RPM just to see how low the engine can go. I think, the most reliable results were with Fuel Needle Valve to normal ( between 2.75 and 3.75 turns open and then I used the Air Valve ( throttle ) and Compression controls to leash the power of the engine.
The snorkel is for the Air Valve ( Throttle ). I keep forgetting which side to turn for what! : ) I know only, when I press on the fishing cord, I can give a lot of " gas " ( air in this case ) as quickly as I want.
Thanks for your reply. As far as the bad aids go, I think but I am not sure, Ether, Kerosene and Castor Oil work very well as an oxidant against bleeding! The bleeding stopped immediately after started. After the test, I just washed hands and : no bleeding! Do not use this as a method of stopping of bleeding! : )
I was so impatient to make the video, so I did not warm the fuel up and the fuel was at freezing temperatures thanks to the John Deere squeeze can with propellants. I think, this is one of the major reasons for the engine to start with such a difficulty.
Another thing : I have found this out : During start up, STOP AND WAIT for 30 seconds after the fuel is loaded in the crankcase to make the fuel settle down in the crankcase and then do a spring start so the fuel is shot up into the upper cylinder. I think this is very useful and I will post this as a separate reply topic.
During start up, STOP AND WAIT
I have found this out : During start up, STOP AND WAIT for 30 seconds AFTER the fuel is loaded in the crankcase to make the fuel settle down in the crankcase and then do a spring start so the fuel is shot up into the upper cylinder.
Ensure the amount of fuel is not as much as to flood the engine.
Ensure the amount of fuel is not as much as to flood the engine.
Re: Micro 12VDC Generator with a Cox .049 Sure Start Diesel Engine
RknRusty wrote:Or a gear on the output shaft that turns another gear which has a pulley bolted to its face.StevenStanleyBayes wrote: Finding elastic tape and trying to run the alternator without too much of a force by the belt because the more the belt pull the higher the wear on the crankcase axel housing
I have an idea of how to decrease the wear of the crankcase axel housing : I do not know whether I can do but a company can easily manufacture a wheel with a rubber tire. The " tire " goes inside the pulley canal ( just like the belt ) where there is no belt. This wheel is " empty " and does not rotate anything. The only thing this wheel does is counters the pull of the belt which pulls the spinning crankshaft axel in the direction towards the dynamo. The empty wheel position and counter tension can be made adjustable by moving the wheel towards the engine pulley or away before securing the wheel with a screw or nut, just like a car alternator. Also, the wheel tension can be defined by a spring which moves the wheel towards the engine pulley. The strength of the string can be selected. The wheel can be mount on a movable arm, controlled by the spring.
Rusty
THANK YOU FOR THIS EXCELLENT SUGGESTION!
Yes, gears will solve the problem. The best, there are dynamos and generators with built in gears. Usually, these are for 100RPM or around use but any gears can be put in a dynamo and a generator. Usually, they are sold sealed but I do not know what else they do. I can imagine there are some where the customer puts the gears and various gears are sold in the pack by the manufacturer. These are usually expensive.
Gears are sold separately but lining them up is very difficult in the out of a company environment. Also, when the gears break, finding them and replacing them is very difficult as opposed to changing the belt.
Yet, gears are better and can be better centered.
Other ways I have found are to center the propeller axel ( an extended one ) with two ball bearings. Requires immense accuracy.
To channel the belt with " empty " wheels in such a way, so the belt touches the engine pulley only on top and bottom with equal force. Teethed belt and pulleys are welcome. Again, not very easy to do in an out of a company environment.
Re: Micro 12VDC Generator with a Cox .049 Sure Start Diesel Engine
do it just like me
directly coupled
then there is almost no wear and the engine bearings will take a lot of the force
directly coupled
then there is almost no wear and the engine bearings will take a lot of the force
robot797- Platinum Member
- Posts : 749
Join date : 2013-07-28
Age : 33
Status Report
Started to make a bracket for the dynamo.
I use Aluminium for the bracket because Aluminium does not affect magnets and magnetic lines, i. e. Aluminium is non ferrous. I even have a scratch pad for the guitar made of Aluminium and the backplate made of Bronze ( also non ferrous ).
However, I do not have any screws except steel. Thus. I stopped and will continue after I go to the shop and get brass screws, nuts and washers.
The problem is : I cannot make a good 90 degree angle with hand tools. I don't even have a big vice. With a big vice or anvil and a hammer, better results can be achieved.
The best way to do this is with a torch or fire where Aluminium can be heated and bent to any shape. I do not have these and do not want to purchase these, although there are inexpensive, ready to use bottle torches where the gun is on the bottle and they are usually for single use although there may be some which are rechargeable.
Managed to make some angle, kind of 90 degrees. Can re twist when done for a fine adjustment.
Problem : the dynamo axel ( the rotor ) is very short thin and cylindrical. Cannot figure out very well how to attach the pulleys. Superglue may be best to be avoided. Extension difficult. Heat shrinks may or may not do.
I use Aluminium for the bracket because Aluminium does not affect magnets and magnetic lines, i. e. Aluminium is non ferrous. I even have a scratch pad for the guitar made of Aluminium and the backplate made of Bronze ( also non ferrous ).
However, I do not have any screws except steel. Thus. I stopped and will continue after I go to the shop and get brass screws, nuts and washers.
The problem is : I cannot make a good 90 degree angle with hand tools. I don't even have a big vice. With a big vice or anvil and a hammer, better results can be achieved.
The best way to do this is with a torch or fire where Aluminium can be heated and bent to any shape. I do not have these and do not want to purchase these, although there are inexpensive, ready to use bottle torches where the gun is on the bottle and they are usually for single use although there may be some which are rechargeable.
Managed to make some angle, kind of 90 degrees. Can re twist when done for a fine adjustment.
Problem : the dynamo axel ( the rotor ) is very short thin and cylindrical. Cannot figure out very well how to attach the pulleys. Superglue may be best to be avoided. Extension difficult. Heat shrinks may or may not do.
Re: Micro 12VDC Generator with a Cox .049 Sure Start Diesel Engine
robot797 wrote:do it just like me
directly coupled
then there is almost no wear and the engine bearings will take a lot of the force
THANK YOU FOR THIS EXCELLENT SUGGESTION TOO!
Yes. This is a good way. There are several posts which show a generator directly connected to the engine. These can be directly coupled as an extension or what they call " pan cake " generators as the coxgen project.
However, I want to be able to gear the generator to the engine and adjust the gears when needed. This is why I have decided to use pulleys and a belt. Also these are supposed to be easier in a non company environment.
I do NOT know neither the engines RPM to energy graphics nor the dynamo's RPM to output energy graphics as these are not available.
Here is the dynamo I have : http://m.ebay.ca/itm/301096305936?_mwBanner=1 I will post this in a different topic. Looks like, after the diode drop of 0.65V to 1V, I need 6500RPM to get 12V AT ZERO LOAD. At higher loads, the dynamo may need to go to 8000RPM or more.
I will make a separate post reply with the subject.
However, I have visually examined the wire of the dynamo. The wire is so thin, I doubt the generator can display more than 0.5A. Also, the dynamo heats up a lot, so a separate fan is welcome and, probably, blowers too. I do not think I can make blowers for the dynamo at for now but I may try to squeeze a tiny fan, either the one I have or I can make one from 1mm Aluminium.
I can also make a, say, 3.5 inch multiblade propeller for the engine from a few 1mm Aluminium double blade propellers but this may be for after I make the initial version of the project.
Sullivan and many Chinese companies make pancake generators and there are very many of them. They are plastic and thus must be light. However, Sullivan and the Chinese charge more for these than a brand new rebuilt ( they use an old housing only, everything else is brand new ) alternator for most any car and truck.
For the record : I love the directly coupled with or without internal to the generator gears, the pancakes, the gear wheel ones and all non belt designs. I cannot easily make this for the prototype. A company can, I do not think I can.
Last edited by StevenStanleyBayes on Wed Mar 04, 2015 5:17 pm; edited 2 times in total
The Dynamo, The Fan and a Possible Self Made Propeller
Here is the dynamo I have : http://m.ebay.ca/itm/301096305936?_mwBanner=1 I will post this in a different topic. Looks like, after the diode drop of 0.65V to 1V, I need 6500RPM to get 12V AT ZERO LOAD. At higher loads, the dynamo may need to go to 8000RPM or more.
I do NOT know neither the engines RPM to energy graphics nor the dynamo's RPM to output energy graphics as these are not available. I would use pulleys which are easy to re adjust.
However, I have visually examined the wire of the dynamo. The wire is so thin, I doubt the generator can display more than 0.5A. Also, the dynamo heats up a lot, so a separate fan is welcome and, probably, blowers too. I do not think I can make blowers for the dynamo at for now but I may try to squeeze a tiny fan, either the one I have or I can make one from 1mm Aluminium.
I can also make a, say, 3.5 inch multiblade propeller for the engine from a few 1mm Aluminium double blade propellers but this may be for after I make the initial version of the project.
I do NOT know neither the engines RPM to energy graphics nor the dynamo's RPM to output energy graphics as these are not available. I would use pulleys which are easy to re adjust.
However, I have visually examined the wire of the dynamo. The wire is so thin, I doubt the generator can display more than 0.5A. Also, the dynamo heats up a lot, so a separate fan is welcome and, probably, blowers too. I do not think I can make blowers for the dynamo at for now but I may try to squeeze a tiny fan, either the one I have or I can make one from 1mm Aluminium.
I can also make a, say, 3.5 inch multiblade propeller for the engine from a few 1mm Aluminium double blade propellers but this may be for after I make the initial version of the project.
Re: Micro 12VDC Generator with a Cox .049 Sure Start Diesel Engine
ANY copper alloy and aluminium is a recipe for electrolytic disaster. Copper will eat aluminium quite quickly.StevenStanleyBayes wrote:Started to make a bracket for the dynamo.
I use Aluminium for the bracket because Aluminium does not affect magnets and magnetic lines, i. e. Aluminium is non ferrous. I even have a scratch pad for the guitar made of Aluminium and the backplate made of Bronze ( also non ferrous ).
However, I do not have any screws except steel. Thus. I stopped and will continue after I go to the shop and get brass screws, nuts and washers.
The problem is : I cannot make a good 90 degree angle with hand tools. I don't even have a big vice. With a big vice or anvil and a hammer, better results can be achieved.
The best way to do this is with a torch or fire where Aluminium can be heated and bent to any shape. I do not have these and do not want to purchase these, although there are inexpensive, ready to use bottle torches where the gun is on the bottle and they are usually for single use although there may be some which are rechargeable.
Managed to make some angle, kind of 90 degrees. Can re twist when done for a fine adjustment.
Problem : the dynamo axel ( the rotor ) is very short thin and cylindrical. Cannot figure out very well how to attach the pulleys. Superglue may be best to be avoided. Extension difficult. Heat shrinks may or may not do.
dinsdale- Account Deactivated by Owner
- Posts : 317
Join date : 2012-02-22
Re: Micro 12VDC Generator with a Cox .049 Sure Start Diesel Engine
StevenStanleyBayes wrote:Here is the dynamo I have : http://m.ebay.ca/itm/301096305936?_mwBanner=1 I will post this in a different topic. Looks like, after the diode drop of 0.65V to 1V, I need 6500RPM to get 12V AT ZERO LOAD. At higher loads, the dynamo may need to go to 8000RPM or more.
That looks like a regular, brushed, electric motor to me. I guess you'll need a separate test rig to characterize its operation as a generator/dynamo.
Surfer_kris- Diamond Member
- Posts : 1905
Join date : 2010-11-20
Location : Sweden
Re: Micro 12VDC Generator with a Cox .049 Sure Start Diesel Engine
StevenStanleyBayes wrote:
I do NOT know neither the engines RPM to energy graphics nor the dynamo's RPM to output energy graphics as these are not available.
Here are some typical power curves for the Cox .049 engines. A Sure Start on glow fuel is probably close to the Babe Bee, while on diesel there might be a little more torque for any given rpm.
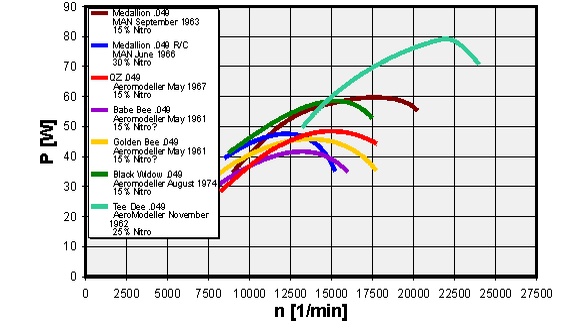
Surfer_kris- Diamond Member
- Posts : 1905
Join date : 2010-11-20
Location : Sweden
Re: Micro 12VDC Generator with a Cox .049 Sure Start Diesel Engine
dinsdale wrote:ANY copper alloy and aluminium is a recipe for electrolytic disaster. Copper will eat aluminium quite quickly.StevenStanleyBayes wrote:Started to make a bracket for the dynamo.
I use Aluminium for the bracket because Aluminium does not affect magnets and magnetic lines, i. e. Aluminium is non ferrous. I even have a scratch pad for the guitar made of Aluminium and the backplate made of Bronze ( also non ferrous ).
However, I do not have any screws except steel. Thus. I stopped and will continue after I go to the shop and get brass screws, nuts and washers.
The problem is : I cannot make a good 90 degree angle with hand tools. I don't even have a big vice. With a big vice or anvil and a hammer, better results can be achieved.
The best way to do this is with a torch or fire where Aluminium can be heated and bent to any shape. I do not have these and do not want to purchase these, although there are inexpensive, ready to use bottle torches where the gun is on the bottle and they are usually for single use although there may be some which are rechargeable.
Managed to make some angle, kind of 90 degrees. Can re twist when done for a fine adjustment.
Problem : the dynamo axel ( the rotor ) is very short thin and cylindrical. Cannot figure out very well how to attach the pulleys. Superglue may be best to be avoided. Extension difficult. Heat shrinks may or may not do.
I have heard Aluminium would prevent corrosion on iron and steel because of reversed potentials but I have never heard of an electrolytic disaster between Copper and Aluminium. So far, they seem to be OK and I have had other cases where I use Copper and Aluminium in electronics and electrical. After all, the best enclosures for electronics and electrical where there are a lot of touching Copper wires is Aluminium.
Regardless, I do take your point, however, I am pretty sure everything will be OK in the next few hundred years or for now.
Aluminium screws and nuts can be used on Aluminium for manufacturing purposes. For the prototype, most anything, except iron based products, such as steel, is OK. Please, note, ONLY iron is ferrous. Obviously, anything which contains iron, such as steel and other alloys is also ferrous to an extent which depends on the concentration of iron.
I agree with you, for production purposes, these things must be taken into account and Aluminium and Copper must not be mixed. I hope I remember this for the future.
Re: Micro 12VDC Generator with a Cox .049 Sure Start Diesel Engine
Surfer_kris wrote:StevenStanleyBayes wrote:Here is the dynamo I have : http://m.ebay.ca/itm/301096305936?_mwBanner=1 I will post this in a different topic. Looks like, after the diode drop of 0.65V to 1V, I need 6500RPM to get 12V AT ZERO LOAD. At higher loads, the dynamo may need to go to 8000RPM or more.
That looks like a regular, brushed, electric motor to me. I guess you'll need a separate test rig to characterize its operation as a generator/dynamo.
As I have been saying, this IS a simple brushed dynamo. Dynamo means a DC generator and not an AC one. Alternator means an AC generator and not a DC one.
There are brushes and there is NO information of the output. Some people say this can only give 16W, others say 100W. On the top of everything, there are a few version of RS555 with different characteristics and there are no markings to say which one I have. I accept this to be the most inexpensive one with the worst characteristics possible.
Thus, the safest way is to put a 0.5A fuse which will allow only 6W at 12V. 1A fuse may be OK and will give 12W at 12V. Some people claim this alternator can only display 1.3A at 12V others say more and some say more can only be achieved with a fan. Regardless of who says what a fan is always a good ide.
I will be happy to get 0.5A at 12V ( 6W ) for the first tests. I do not want to test the dynamo with an electric drill or the engine as I may damage the unknown generator when I put various of loads. All sources, however, show 0.6A at 12V to be safe.
For these who are interested, another, slightly more expensive purchase, is either YAF 54 ( already mentioned extensively ) or other Mabuchi motors ( RS555 is one of their motor generators ) or JOHNSON BRUSHED DYNAMOS. There is one which is 70W and is good for this project but I did not want to pay money for this. Sold by a US seller on eBay. Made in China. Johnson is a US company. I am not sure whether they design dynamos any more. Most likely these are old design which continues to be made in China or Johnson may have discontinued these and there are some old products around online still sold until available.
DYNAMOS AND ALTERNATORS ARE THE DUMBIEST ELECTRICAL DEVICES EVEN DUMBIER THAN A TRANSFORMER ( THERE ARE ACCURATE MEASUREMENT TRANSFORMERS WHICH ARE " ADVANCED " AS COMPARE TO THE OTHER ONES AND THE GENERATORS ) AND THERE MUST BE MANY OF THESE AVAILABLE ALL OVER THE PLACE FOR A DOLAR OR TWO. THERE IS NOTHING INSIDE TO PAY FOR.
The reality is there are not very many around and some of them have ridiculous prices. HENCE THE RS555.
You are welcome to use Johnson in case you so desire. Google search with " Johnson 70W DC Generator, eBay ". Or, here is the link : http://www.ebay.com/itm/280776426221?_trksid=p2060778.m1438.l2648&ssPageName=STRK%3AMEBIDX%3AIT
Re: Micro 12VDC Generator with a Cox .049 Sure Start Diesel Engine
Surfer_kris wrote:StevenStanleyBayes wrote:
I do NOT know neither the engines RPM to energy graphics nor the dynamo's RPM to output energy graphics as these are not available.
Here are some typical power curves for the Cox .049 engines. A Sure Start on glow fuel is probably close to the Babe Bee, while on diesel there might be a little more torque for any given rpm.
Thank you very much for this information. Any information is better than no information at all.
The only other information I have is the RPM range of Cox .049 SureStart Diesel Engine, which is 4000 to 13000 ( 12000 more likely ) RPM : http://coxengines.ca/cox-.049-rc-diesel-engine.html Scroll down and look to the right.
The other information I have is the maximal power of this engine is 40 to 50W, 50W is more cited.
Because diesel fuel is more powerful and as depends of the fuel component mixture ( which can be varied a lot ), I expect the engine to have a flatter power RPM response at RPM lower than the RPM where the maximal power is displayed. I expect but I am not sure the engine to reach maximal power at 6000 to 8000 RPM. I do not know, though. I expect the power output to decrease significantly after 9000 RPM. Again, I do not know.
Status Report
The attachment of the dynamo is almost ready. Have not purchased the brass screws yet.
May attach the dynamo to be able to work with 5 or 6 inch propellers. Intend to use the Cox 3.5 inch triple blade propeller which I expect to provide good aeration at low RPM. Can always be replaced. The dynamo can always be readjusted too.
An Aluminium angle bracket has been made on which a wooden bed is mounted to hold the dynamo and then an Aluminium top bracket with brass screws can be used to hold the dynamo stable.
The angle bracket will be screwed onto the enclosure with brass screws too. There will not be ferrous materials in close proximity to the dynamo.
May attach the dynamo to be able to work with 5 or 6 inch propellers. Intend to use the Cox 3.5 inch triple blade propeller which I expect to provide good aeration at low RPM. Can always be replaced. The dynamo can always be readjusted too.
An Aluminium angle bracket has been made on which a wooden bed is mounted to hold the dynamo and then an Aluminium top bracket with brass screws can be used to hold the dynamo stable.
The angle bracket will be screwed onto the enclosure with brass screws too. There will not be ferrous materials in close proximity to the dynamo.
Re: Micro 12VDC Generator with a Cox .049 Sure Start Diesel Engine
StevenStanleyBayes wrote:
Because diesel fuel is more powerful and as depends of the fuel component mixture ( which can be varied a lot ), I expect the engine to have a flatter power RPM response at RPM lower than the RPM where the maximal power is displayed. I expect but I am not sure the engine to reach maximal power at 6000 to 8000 RPM. I do not know, though. I expect the power output to decrease significantly after 9000 RPM. Again, I do not know.
The torque will be a little higher on diesel I guess but the rpm dependence is probably very similar. I.e. the torque curve is fairly flat and that gives you a nearly linear power curve (that goes through the origin). The maximum power point I guess is limited mainly by the internals, such as size of intake and the reed, transfer channel size etc. So that will not change much when converting to diesel fuel.
You can easily measure power curves by using different sized propellers. The propellers should be load calibrated in order to have some accuracy, but you can get a rough estimate by using regular props too.
Here are some of my own data for the Queen Bee engine converted to diesel by using an RJL 09 conversion head;

Surfer_kris- Diamond Member
- Posts : 1905
Join date : 2010-11-20
Location : Sweden
Re: Micro 12VDC Generator with a Cox .049 Sure Start Diesel Engine
Surfer_kris wrote:StevenStanleyBayes wrote:
Because diesel fuel is more powerful and as depends of the fuel component mixture ( which can be varied a lot ), I expect the engine to have a flatter power RPM response at RPM lower than the RPM where the maximal power is displayed. I expect but I am not sure the engine to reach maximal power at 6000 to 8000 RPM. I do not know, though. I expect the power output to decrease significantly after 9000 RPM. Again, I do not know.
The torque will be a little higher on diesel I guess but the rpm dependence is probably very similar. I.e. the torque curve is fairly flat and that gives you a nearly linear power curve (that goes through the origin). The maximum power point I guess is limited mainly by the internals, such as size of intake and the reed, transfer channel size etc. So that will not change much when converting to diesel fuel.
You can easily measure power curves by using different sized propellers. The propellers should be load calibrated in order to have some accuracy, but you can get a rough estimate by using regular props too.
Here are some of my own data for the Queen Bee engine converted to diesel by using an RJL 09 conversion head;
This is very interesting. Thank you for this post.
Cox .049 SureStart Diesel cannot reach the speeds your engine can. The RPM which the engine can reach for sure is 10000. Whether the engine reaches anywhere from 10000 to 13000 depends on the load, fuel and temperature. I will probably never test the engine at such huge RPM or, in case I do, this will be in a very remote future because I am afraid I may damage the engine. I prefer not to reach the maximal power output and not to test what happens thereafter but to keep the engine nice and safe.
Slow burning fuel may not be able to reach high RPM and the power output may be very low at high RPM and reach maximal power at lower RPM. To make the fuel slow burning, I think, one may need to decrease the amount of Ether and increase the amount of Kerosene. Thus, per single combustion at lower RPM, the engine may get more power from the power giving Kerosene, but, at very high RPM, only some portion of Kerosene would burn and, regardless of more combustions per second, the power may decrease significantly because the power of one combustion decreases incredibly significantly.
Again, I just say what I think and not what is. I do not have a way to measure the output and I have only two known loads ( only two propellers ) which may not be the best way to generalise.
A good way to measure the power output of the engine would be a somewhat known loud, for example, a dynamo or an alternator with a known response, which I do not have.
With a dynamo with unknown response, the overall energy of the system can be measured just by multiplying current by voltage but there is no way to know how much energy the dynamo looses in order to say how much the engine gives.
Status Report
The bracket to attach the dynamo to the enclosure has been made and looks OK.
The greatest difficulty ( other than the engine ) so far, as expected, was the pulley and the pulley attachment.
The dynamo, as you can see on the previously posted link, has a cylindrical axel extension which is very flat and only 9mm long and 2mm in diameter. Some people suggest to put an extension which I do not have. I may be able to find a copper pipe with a 2mm diameter but I do not know whether AliExpress or anyone sells these. Then, I can press fit the pipe and crimp. Then, I can flatten the pipe after the axel and press fit pulleys there. I can also put copper wires along the pipe and press fit plastic pulleys onto the pipe. I thought whether to do this with the axel only.
Instead, here is what I have done :
I took two identical pulleys which were very tight and filed one of the rims of each of them off. This way they can be put one next to the other and make one thicker pulley. Then, I installed a fuel pipe on the top of the axel and installed one of the pulleys on the fuel pipe. The installation flattened the fuel line. I installed a heat shrink over the fuel line ( hose ) and I heated the heat shrink tube. Then, I installed the other pulley. Then I glued the second pulley to the heat shrink with supper glue. Then, I glued the two pulleys one to another by putting glue on top of where they meet. Then I glued a fan to the heat shrink.
Thus, now, the dynamo has a fuel line hose over the axel, half of a pulley press fit to this fuel line hose, a heat shrink tube, the other half of the pulley press fit and super glued to the heat shrink tube, the two half pulleys super glued to each other and a fan super glued to the heat shrink tube outside of the axel.
Can rotate the dynamo by hand just by rotating the pulley.
However, at some load and some RPM, I am not sure whether :
1. The first half pulley would not cut through the fuel line hose and spin around the axel without rotating the axel.
2. The same for the second half pulley over the heat shrink tube and the fuel line hose.
3. The fan would not pull all out or break lose or damage the tube and the hose.
I know there are Aluminium pulleys with screws to attach to an axel but I have never seen these attached to a CYLINDRICAL axel made of steel.
May I ask you this : how do you all think a pulley can fit on a flat, cylindrical, shiny, super tough stainless steel axel?
Also, do you know of any extension for these and how does the extension attach to the axel?
Welding and soldering is out of question.
The greatest difficulty ( other than the engine ) so far, as expected, was the pulley and the pulley attachment.
The dynamo, as you can see on the previously posted link, has a cylindrical axel extension which is very flat and only 9mm long and 2mm in diameter. Some people suggest to put an extension which I do not have. I may be able to find a copper pipe with a 2mm diameter but I do not know whether AliExpress or anyone sells these. Then, I can press fit the pipe and crimp. Then, I can flatten the pipe after the axel and press fit pulleys there. I can also put copper wires along the pipe and press fit plastic pulleys onto the pipe. I thought whether to do this with the axel only.
Instead, here is what I have done :
I took two identical pulleys which were very tight and filed one of the rims of each of them off. This way they can be put one next to the other and make one thicker pulley. Then, I installed a fuel pipe on the top of the axel and installed one of the pulleys on the fuel pipe. The installation flattened the fuel line. I installed a heat shrink over the fuel line ( hose ) and I heated the heat shrink tube. Then, I installed the other pulley. Then I glued the second pulley to the heat shrink with supper glue. Then, I glued the two pulleys one to another by putting glue on top of where they meet. Then I glued a fan to the heat shrink.
Thus, now, the dynamo has a fuel line hose over the axel, half of a pulley press fit to this fuel line hose, a heat shrink tube, the other half of the pulley press fit and super glued to the heat shrink tube, the two half pulleys super glued to each other and a fan super glued to the heat shrink tube outside of the axel.
Can rotate the dynamo by hand just by rotating the pulley.
However, at some load and some RPM, I am not sure whether :
1. The first half pulley would not cut through the fuel line hose and spin around the axel without rotating the axel.
2. The same for the second half pulley over the heat shrink tube and the fuel line hose.
3. The fan would not pull all out or break lose or damage the tube and the hose.
I know there are Aluminium pulleys with screws to attach to an axel but I have never seen these attached to a CYLINDRICAL axel made of steel.
May I ask you this : how do you all think a pulley can fit on a flat, cylindrical, shiny, super tough stainless steel axel?
Also, do you know of any extension for these and how does the extension attach to the axel?
Welding and soldering is out of question.
Pulleys, Gears and Straight Coupling
In case the engine and the generator match in their RPM, power and voltage characteristics, then straight connecting the two axels looks to be the best to do. And is. This gives a logical gear ratio of 1 to 1 and the generator can be positioned in front of the engine.
Otherwise gear wheels ( with or without stabilizers ) either coupled to each other or connected with a chain is the best solution.
Pulleys and a belt look to be the worst solution but have these advantages :
1. Supposed to be the easiest to do ( unless the generator has a flat axel and pulleys with screws and axel extension are not available ) and the most inexpensive.
2. Allow the belt to be removed, the engine started and heated up, then stopped, then the belt re installed and, then the engine started again.
3. Allow easy recalculation of gears and quick re installment ( under normal circumstances ) of different pulleys for a different job.
4. Protect the engine : in case of a problem, the belt will just slide over and not load the engine as much. Also, allow for the belt tension can be adjusted as per the desire of the user. This can be done either by moving the generator ( like in some cars ) or by an empty spring ( and or re adjustable ) pulley.
5. Easy to replace ( under normal circumstances ).
Straight coupling can perform 2 in case designed for an easy decoupling. Gears can perform 2 and 3 in case designed for an easy decoupling and replacement. Specially designed soft connection and or soft gears can introduce 4 to straight coupling and gear wheels too.
Otherwise gear wheels ( with or without stabilizers ) either coupled to each other or connected with a chain is the best solution.
Pulleys and a belt look to be the worst solution but have these advantages :
1. Supposed to be the easiest to do ( unless the generator has a flat axel and pulleys with screws and axel extension are not available ) and the most inexpensive.
2. Allow the belt to be removed, the engine started and heated up, then stopped, then the belt re installed and, then the engine started again.
3. Allow easy recalculation of gears and quick re installment ( under normal circumstances ) of different pulleys for a different job.
4. Protect the engine : in case of a problem, the belt will just slide over and not load the engine as much. Also, allow for the belt tension can be adjusted as per the desire of the user. This can be done either by moving the generator ( like in some cars ) or by an empty spring ( and or re adjustable ) pulley.
5. Easy to replace ( under normal circumstances ).
Straight coupling can perform 2 in case designed for an easy decoupling. Gears can perform 2 and 3 in case designed for an easy decoupling and replacement. Specially designed soft connection and or soft gears can introduce 4 to straight coupling and gear wheels too.
Thesis Update
The thesis has been appended with discussed here topics :
Thesis : http://www.steven-stanley-bayes.com/Cox%20.049%20SureStart%20Diesel.doc
Pictures : http://www.steven-stanley-bayes.com/Pictures%20of%20the%20Engine%20and%20the%20Stand.doc
Video : https://www.youtube.com/watch?v=Y7FfparKL78&list=UUiFdItymm78mcEB5Qlu67tg
Thesis : http://www.steven-stanley-bayes.com/Cox%20.049%20SureStart%20Diesel.doc
Pictures : http://www.steven-stanley-bayes.com/Pictures%20of%20the%20Engine%20and%20the%20Stand.doc
Video : https://www.youtube.com/watch?v=Y7FfparKL78&list=UUiFdItymm78mcEB5Qlu67tg
Re: Micro 12VDC Generator with a Cox .049 Sure Start Diesel Engine
StevenStanleyBayes wrote:Surfer_kris wrote:StevenStanleyBayes wrote:
Because diesel fuel is more powerful and as depends of the fuel component mixture ( which can be varied a lot ), I expect the engine to have a flatter power RPM response at RPM lower than the RPM where the maximal power is displayed. I expect but I am not sure the engine to reach maximal power at 6000 to 8000 RPM. I do not know, though. I expect the power output to decrease significantly after 9000 RPM. Again, I do not know.
The torque will be a little higher on diesel I guess but the rpm dependence is probably very similar. I.e. the torque curve is fairly flat and that gives you a nearly linear power curve (that goes through the origin). The maximum power point I guess is limited mainly by the internals, such as size of intake and the reed, transfer channel size etc. So that will not change much when converting to diesel fuel.
You can easily measure power curves by using different sized propellers. The propellers should be load calibrated in order to have some accuracy, but you can get a rough estimate by using regular props too.
Here are some of my own data for the Queen Bee engine converted to diesel by using an RJL 09 conversion head;
This is very interesting. Thank you for this post.
Cox .049 SureStart Diesel cannot reach the speeds your engine can. The RPM which the engine can reach for sure is 10000. Whether the engine reaches anywhere from 10000 to 13000 depends on the load, fuel and temperature. I will probably never test the engine at such huge RPM or, in case I do, this will be in a very remote future because I am afraid I may damage the engine. I prefer not to reach the maximal power output and not to test what happens thereafter but to keep the engine nice and safe.
Slow burning fuel may not be able to reach high RPM and the power output may be very low at high RPM and reach maximal power at lower RPM. To make the fuel slow burning, I think, one may need to decrease the amount of Ether and increase the amount of Kerosene. Thus, per single combustion at lower RPM, the engine may get more power from the power giving Kerosene, but, at very high RPM, only some portion of Kerosene would burn and, regardless of more combustions per second, the power may decrease significantly because the power of one combustion decreases incredibly significantly.
Again, I just say what I think and not what is. I do not have a way to measure the output and I have only two known loads ( only two propellers ) which may not be the best way to generalise.
A good way to measure the power output of the engine would be a somewhat known loud, for example, a dynamo or an alternator with a known response, which I do not have.
With a dynamo with unknown response, the overall energy of the system can be measured just by multiplying current by voltage but there is no way to know how much energy the dynamo looses in order to say how much the engine gives.
Also, I do not think putting more Kerosene instead of Ether would make the fuel thicker and reduce the suction, although, Kerosene looks to be slightly thicker than Ether.
Re: Micro 12VDC Generator with a Cox .049 Sure Start Diesel Engine
StevenStanleyBayes wrote:
Cox .049 SureStart Diesel cannot reach the speeds your engine can. The RPM which the engine can reach for sure is 10000. Whether the engine reaches anywhere from 10000 to 13000 depends on the load, fuel and temperature. I will probably never test the engine at such huge RPM or, in case I do, this will be in a very remote future because I am afraid I may damage the engine. I prefer not to reach the maximal power output and not to test what happens thereafter but to keep the engine nice and safe.
There is nothing huge about 10000-13000rpm for our two-stroke model engines. On the contrary these are very modest revs. Most glow engines for instance will overheat if they are propped with a too high load and forced to stay at or below 15000rpm. Diesel engines are a little different and they can quite happily run at around 10000rpm but not much lower (at full throttle). So at full power from the generator I think the engine will be most happy if it revs at around 10000-13000rpm.
For a given prop and rpm you can calculate the power the engine makes by using an excel sheet from Pe Rivers who worked at MVVS. He has passed away but a similar calculator can still be found here; excel sheet
If your engine makes 10000rpm on a 6x3 prop it is putting out about 16W in order to do so. Props from different makes are all a little different in their load, but this gives you a good estimation. With a nearly constant torque curve, this engine would then make a staggering 8W at 5000rpm.

This is assuming that it is able to run at 5000rpm with full throttle without overheating....
Surfer_kris- Diamond Member
- Posts : 1905
Join date : 2010-11-20
Location : Sweden
Re: Micro 12VDC Generator with a Cox .049 Sure Start Diesel Engine
Surfer_kris wrote:StevenStanleyBayes wrote:
Cox .049 SureStart Diesel cannot reach the speeds your engine can. The RPM which the engine can reach for sure is 10000. Whether the engine reaches anywhere from 10000 to 13000 depends on the load, fuel and temperature. I will probably never test the engine at such huge RPM or, in case I do, this will be in a very remote future because I am afraid I may damage the engine. I prefer not to reach the maximal power output and not to test what happens thereafter but to keep the engine nice and safe.
There is nothing huge about 10000-13000rpm for our two-stroke model engines. On the contrary these are very modest revs. Most glow engines for instance will overheat if they are propped with a too high load and forced to stay at or below 15000rpm. Diesel engines are a little different and they can quite happily run at around 10000rpm but not much lower (at full throttle). So at full power from the generator I think the engine will be most happy if it revs at around 10000-13000rpm.
For a given prop and rpm you can calculate the power the engine makes by using an excel sheet from Pe Rivers who worked at MVVS. He has passed away but a similar calculator can still be found here; excel sheet
If your engine makes 10000rpm on a 6x3 prop it is putting out about 16W in order to do so. Props from different makes are all a little different in their load, but this gives you a good estimation. With a nearly constant torque curve, this engine would then make a staggering 8W at 5000rpm.![]()
This is assuming that it is able to run at 5000rpm with full throttle without overheating....
I agree the maximal power will be at higher RPM but I cannot imagine to be at around 10000 RPM which is stated to be very close to the maximal RPM.
Heating at low RPM is a problem which I expect and, hopefully, I would be wrong. I understand the propeller will take power from the engine. Initially, I will run the engine with two propellers : an 8 inch double blade as a back up and a 3.5 inch triple blade as the preferred one. I also have an option to use big blade quadruple fan, around 4 inches diameter.
I have also mentioned the electrical blowers which I am not sure whether would be powerful enough.
By examining the propellers, I think the maximal aeration a propeller can give to an engine is directed towards the engine and slightly to the right ( looked from the pilot seat ). Thus, I think to put the electric blower to the left of the engine, blowing towards the left side of the engine ( looked from the pilot seat ) and the back of the engine too.
To reduce the heat, I will use rich mixture and not very high compression which will reduce the power.
The only reason to try to do whatever I can to avoid running the engine at high RPM is to avoid the wear of the engine. Otherwise, there is no problem and I can always do so.
Running the engine with more powerful diesel ( more Kerosene ) will also increase the temperature.
Also, the adjustment of the engine depends on the application. In some applications, for example to run a USB powered device, the engine needs to provide just 2.5W because, as mentioned, the USB specifications state a USB powered device must not take more than 0.5W at 5V.
This is why I like the freedom of having three adjustments : the mixture, the amount of fuel and air and the compression.
The 8 inch propeller not only consumes energy and room but is very inconvenient to work with. With a 3.5 inch propeller, one can put hands over the propeller to adjust the controls. More blades will consume more power BUT will provide extremely good aeration with no significant consumption of real estate.
I have to run the engine to see.
Note : the inexpensive RS555 generator, when run as a motor, has the highest efficiency at 12V, 0.6A ( 7.2W ). This is around 68%. The generator may go to 40% at other loads. This means more than half of what the engine makes would be lost.
Reduction of Immediate Stress
An immediate stress may or may not be a problem because of the internal impedance of the generator and the capacitor of the system as well as the impedance of a load, I. e. when the load is switched to consume more, the generator is expected to slowly put more load on the engine and not immediately stress the engine.
However, I have had an idea how to simply make this delay and slow increase even slower : I may put a potentiometer before than the capacitor which can be turned by the user to maximum and then slowly decreased to zero. This way, the generator will slowly increase the load to the engine and, even better, the engine can be readjusted on one or more occasions before the potentiometer is turned to zero.
However, I have had an idea how to simply make this delay and slow increase even slower : I may put a potentiometer before than the capacitor which can be turned by the user to maximum and then slowly decreased to zero. This way, the generator will slowly increase the load to the engine and, even better, the engine can be readjusted on one or more occasions before the potentiometer is turned to zero.
Re: Micro 12VDC Generator with a Cox .049 Sure Start Diesel Engine
Your engine is certainly capable of reliably turning at better than 10,000rpm. I'd not worry up to about 17,000+.
On the cooling front, I think you may be overdoing it somewhat. Consider the Cox car engines. THey have a small heat sink that clamps to the upper cylinder/glow head, and is about 1.25 x 2.5" of finned aluminum, maybe 3/8" thick at best. Their cooling air is provided by a very poor 3 bladed fan about 1.5" in diameter, at the end of the drive shaft, or by a small impeller with tiny 1/4" blades, mounted to the flywheel. They provide decent cooling and acceptable life.
Ran one yesterday in my Sandblaster...
J
On the cooling front, I think you may be overdoing it somewhat. Consider the Cox car engines. THey have a small heat sink that clamps to the upper cylinder/glow head, and is about 1.25 x 2.5" of finned aluminum, maybe 3/8" thick at best. Their cooling air is provided by a very poor 3 bladed fan about 1.5" in diameter, at the end of the drive shaft, or by a small impeller with tiny 1/4" blades, mounted to the flywheel. They provide decent cooling and acceptable life.
Ran one yesterday in my Sandblaster...
J
JasonB- Silver Member
- Posts : 60
Join date : 2015-03-04
Location : Cape Spencer, NB, Canada
Page 7 of 31 • 1 ... 6, 7, 8 ... 19 ... 31

» car engine diesel??? (aka generator V3)
» RC Cars Cox 0.49 (Cox Stocker Kyosho f1,beetle) Killer Bee Backplate New Video!
» Norvel Handi-Start Micro Electric Starter
» 3.5 cc diesel needs needle valve
» little generator
» RC Cars Cox 0.49 (Cox Stocker Kyosho f1,beetle) Killer Bee Backplate New Video!
» Norvel Handi-Start Micro Electric Starter
» 3.5 cc diesel needs needle valve
» little generator
Page 7 of 31
Permissions in this forum:
You cannot reply to topics in this forum